When large Jet Airplanes land on a runway, their tires shred leaving impregnated rubber in the grooves of the asphalt.
When enough Jets land, the rubber build up grows higher and higher until finally the rubber is higher than the asphalt and the planes loose traction and can then easily slip and slide around instead of rolling straight along.
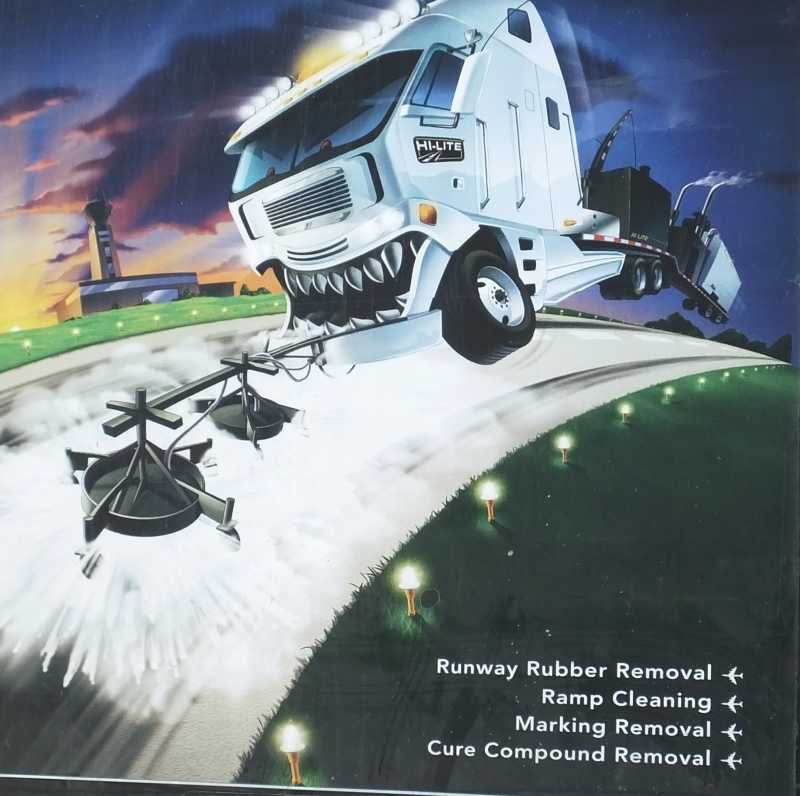
So this company goes in and scrubs the runways with super high pressure water and sucks up the loose soggy rubber pieces in a giant wet vacuum cleaner.
Giant because the whole tractor trailer is scrubbing and sucking as it rolls along the runway while the Jet Planes sit still and can't take off or land while their runway is being vacuumed.
So the runway is closed down and the airport isn't making any money on a runway not being used.
So they call this company and pay them because they can clean a runway faster and better than anyone in the world.
Its very important they finish on time and within their schedule.
Friday night they called me and wanted me welding Saturday morning so their truck could leave out on Sunday morning to head to another airport already scheduled and waiting for them.
ABOVE: That 1,000 gallon clean water tank has a hole in it just behind his chest area.
BELOW: Now that he is out of the way, you can see the hole and its covered with a sealant patch they had hoped would stop the leak of water, but it failed.
Its time to step up the quality of the repair and weld a hefty thick aluminum patch over it and be done with it.
Welding the hole itself would be a problem as their gooey sealant filled it all the way through into the inside of the tank, and their goo would burn and contaminate the weld process.
However welding a large patch around it would solve the problem without us having to weld through their goo which would cause the welds to fail.
So I'm not going to weld the hole itself, but instead weld a large patch around it while my welding is staying in clean metal all the time guaranteeing strong lasting welds.
My helper Ben Gainous has been up there cleaning the area I am going to weld a patch on. I'm welding new aluminum plate, and welding it onto freshly cleaned metal which will produce the highest quality.
I have special secret abrasive wheels that will take off 20 thousandths of an inch and get me back into virgin metal never before exposed, without removing more metal than what needs to go away.
Welding into dirty metal that's been exposed to the elements for ages, produces weak short lived welds ( at least in the world of aluminum).
I'm putting in tack welds at bottom middle, bottom right, top right, and top middle. The tacks will hold the 3/8" aluminum plate in place while I weld it deep and long.
Now the patch is in place, I've tack welded the corners, and am now beginning a full pass along the bottom, starting from the middle and moving to the bottom right.
That's a first pass for good penetration. But since I wanted guaranteed leak protection, it will get a 2nd pass for additional assurance before I am finished with it.
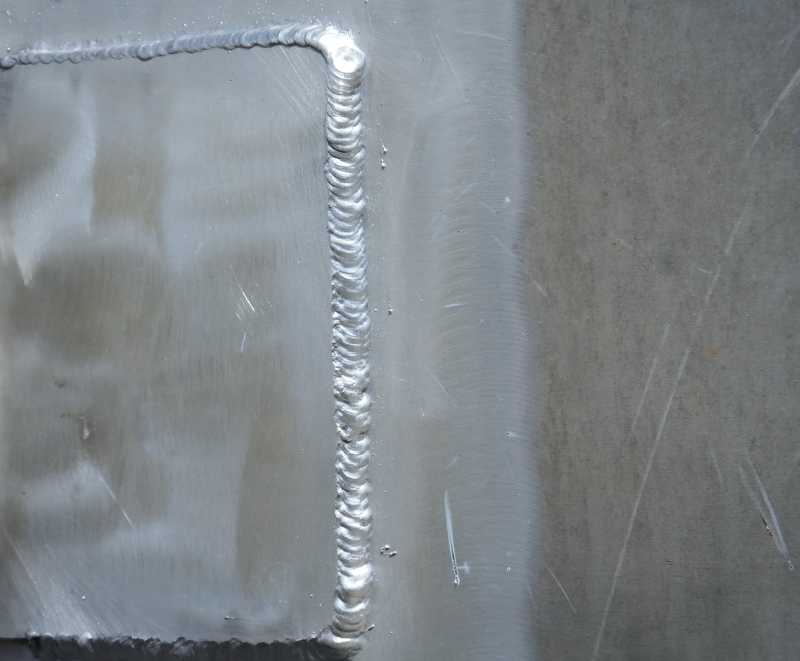
BELOW: Now the next problem. That tank was supposed to be flat and straight across. It was not.
The center of the tank bowed out more in the middle than the rest of the tanks wall. So Now my 3/8" flat patch, when it fit one side of the tank, would not fit the other side of the tank simultaneously.
Either side I made it snug to, would lift the other side of the patch away from the tank about 1". A little tiny 1" seesaw action.
So I aim to bend that aluminum patch plate in the middle and folds its left side over to get a snug fit. But thick aluminum plate does not like being bent, unlike steel plate which doesn't mind.
I will have a stress point right down the middle of the patch where it's bent, which will make it very weak as the metal is stretched and left under stress.
Heating it with a torch will help some, but not totally.
Later I will cut a groove right down the middle of the patch and relieve the stress so it can naturally stretch into place, and then weld/fill in the groove with new aluminum that is not stretched and stressed.
My welding gear is very portable, I can even roll my rig down a 1,000 foot dock and up onto a yacht and into its engine room.
All other guys (lady's too?) that have mobile welding service, their welders are so big and heavy they never leave the truck. So if their truck can't get right next to what they are welding on, they can't get to it.
I have actually welded on a 8th floor balcony. None of my competition could get their trucks up there.
My helper Ben cuts the groove down the middle of the patch. This groove he is cutting is removing the stretched aluminum from the bend that is under tension and being stressed.
Then I come along and weld it back in with fresh aluminum that has no stress and has not been bent.
Filling in my groove from bottom middle to top middle.
A little cleaning with a stainless steel wire brush to remove the soot, and all is well.
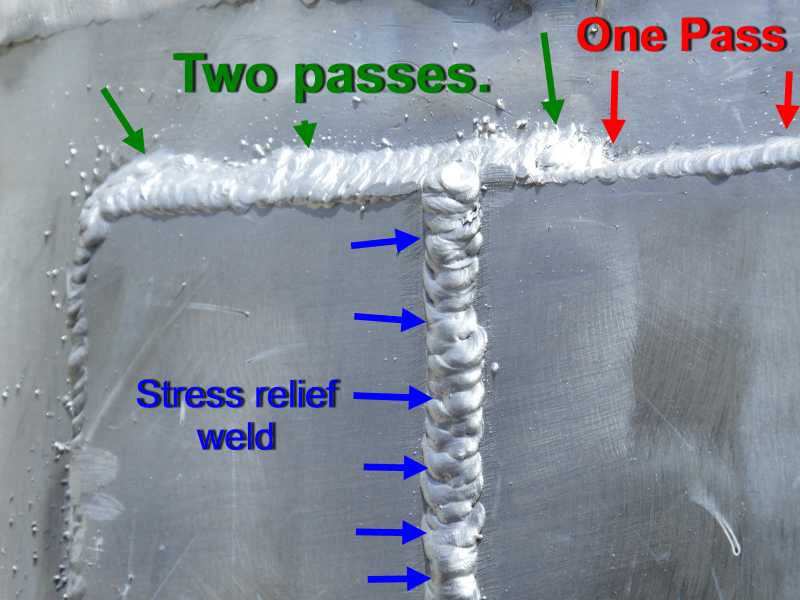
The 1st pass I want to be pretty because I am focusing on weld penetration into the joints. I want it very tight and focused.
But on pass # 2 and 3, penetration is not the issue at hand any more. I am putting down a lot of cover metal as an assurance there are no pin holes to leak through.
So on pass 2 and 3, a pretty looking weld has no value, but a large cover pass does. Now its not about quality of the weld, but all about quantity of weld laid down.
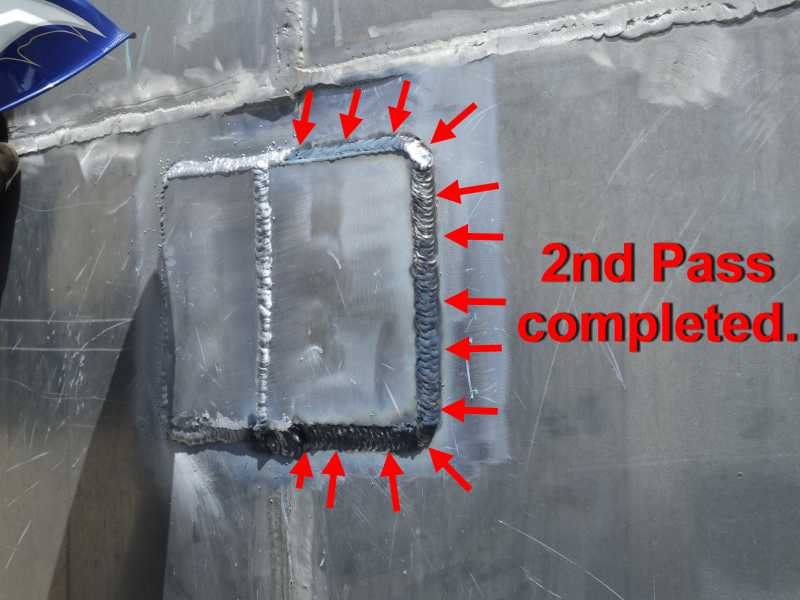
Every area got two passes as a minimum, and a couple of places got three passes where the tank didn't fit flush and tight to the perfectly flat patch.
Mobile, portable welding is not cheap. If you want to save money, bring it to my shop. But if for whatever reason it can't come to my shop, me, my tools and welders can come to your urgent project.